Copper fins are used for a variety of heat exchanger applications. They allow for efficient heat transfer and reduce energy loss. The copper used for copper fins has superior strength and conductivity. However, they are subject to galvanic corrosion.Galvanic action occurs when the tubes or the fins are exposed to corrosive airstreams. This can lead to harmful side effects for building occupants. A protective coating can be added to the fin or the tube to prevent corrosion. Choosing the best fin and tube type can be very important to the success of your product.
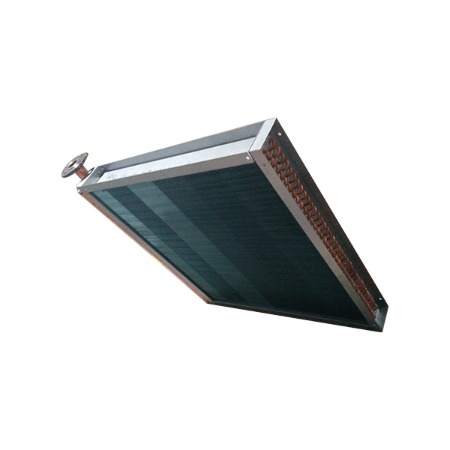
There are three primary types of coils. Aluminum, copper, and stainless steel. Steel is a low cost material that performs well in rough service applications. In addition, it can be formable. Stainless steel has a lower heat transfer co-efficient, but it also has a strong tensile strength.Aluminum and copper fins can be applied to tubes to make condensing coils. Aluminum is the most common and is less expensive than copper. Copper is more expensive, but it offers a superior rate of heat exchange.
If your application requires the best heat transfer, copper is the way to go. Aluminum is a very affordable option, but its ability to bend and form isn't as great as that of copper. Copper coils will maintain their high energy efficiency for longer periods of time. It's also resistant to formicary corrosion.